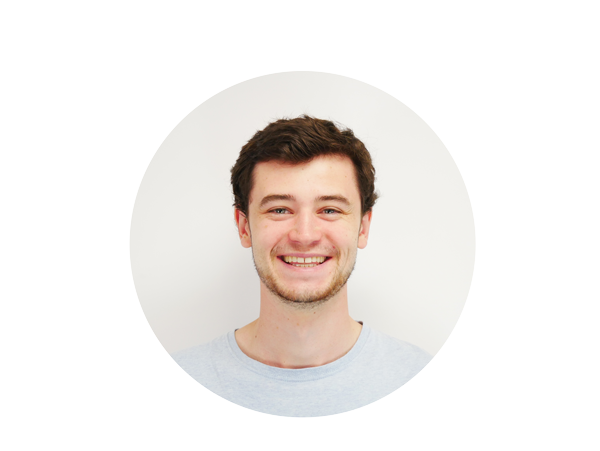
Written by Will Hardy
05/10/2022
Revo ObXidian™ by E3D: Everything you need to know
TL;DR: Years of research and development have gone into Revo ObXidian, making it the most hotly anticipated nozzle in 3D printing history. Guess what, it’s available to order right now!
Here at E3D, it has felt at times like the entire 3DP community has been… not so patiently awaiting ObXidian. In fact, we’ve been inundated with requests for an abrasion-resistant Revo solution since well before we’d even started shipping our new ecosystem. At this point ObXidian is, without a doubt, our most requested (/demanded!) product ever.
Can we blame you? Definitely not! When it comes to ObXidian, there’s a lot to be excited about. So, if you aren’t one of the people flooding our socials with ‘ObXidian WHEN?’ comments, let us explain why ObXidian has everyone so animated. Trust us, it's a game changer.
ObXidian Nozzles are supported by three pillars of performance. Thermal conductivity, non-stick and of course, wear resistance. In this blog we’ll break down what each of these mean and explain why they matter.
Thermal Conductivity
Hardened steel Nozzles like Nozzle X can require you to bump up your HotEnd temperature by around 10 degrees to achieve the same results as when printing with standard brass. It’s a nightmare for OEMs, who invest hours perfecting print profiles in their slicers. When customers install hardened nozzles and forget to change their slicer settings, it leads to print quality issues, clogging and precious time lost for everyone involved.
If you’re wondering why you need to raise your temperatures, it’s because the temperature that the printer is actually trying to maintain is the temperature at the sensor and not what is being reached by the plastic flowing through the HotEnd. When you change the nozzle material, which is between the heater and the plastic (not the heater and the sensor) the plastic won't necessarily see the same temperature anymore, due to the new material's weaker ability to transmit the heat from the heater block through to the plastic. So, when you offset your HotEnd temperature, what you're actually doing is artificially inflating the temperature elsewhere in the system to try and achieve the same results in the plastic.
ObXidian’s copper-alloy construction means you no longer need to spend time fiddling with temperature values to account for the weaker thermal performance of other abrasion-resistant nozzle offerings. Simply select the profile you would use for your brass nozzles and hit print. A true drop-in replacement for your brass nozzles.

Non-Stick
A common occurrence with FDM printing is the little ‘accumulations’ of material that build up on the nozzle. The accumulations gradually build up until they eventually fall off and are deposited in your printed part, at best leading to shoddy print quality and at worst causing a print failure. PETG is one of the worst materials for this! The larger the build-up on the nozzle, the larger the print artefact. If the build-up is particularly bad, it can also lead to a full-on HotEnd engulfing blob.
The non-stick coating on ObXidian helps the plastic accumulations drop off when at a much smaller size. Instead of leaving large blobs of discoloured filament in random spots in your print, ObXidian will continually deposit the filament that is building up. Making it much less likely to lead to print artefacts. The coating also makes filament build ups much easier to clean off than with standard brass nozzles.

Brass Revo Nozzle
A brass Revo Nozzle after a 14-hour print with some of the stickiest PETG we could find!

ObXidian Revo Nozzle
An ObXidian Revo Nozzle after a print with the same G-code
Nozzle X vs ObXidian
Nozzle X also has a non-stick coating, but it’s fair to say it doesn't really repel polymers. We advise against using brass brushes or even paper towels to clean Nozzle X, as these quickly wear away its delicate non-stick coating.
ObXidian features a new E3DLC™ coating. What is E3DLC? - We hear you ask
Diamond Like Carbon (DLC) coatings harness the strength of diamond bonds, the hardest material on Earth, in a lattice with graphite, to form a strong, wear-resistant coating. The DLC coating also offers many other intrinsic benefits; such as low friction, chemical resistance and thermal stability. DLC coatings are not all the same, depending on composition and manufacturing process. The E3DLC coating has been custom designed at the atomic level to offer an unparalleled combination of wear resistance with anti-sticking properties.
There are a number of different ways that thin-film coatings such as DLC can be applied to components. If you read our recent blog about some of the challenges we've been facing while developing ObXidian, you will have seen that E3DLC is applied by plasma-enhanced chemical vapour deposition (or PECVD). If you're interested, this video gives a fantastic explanation as to how that technology works. Introduction to PECVD.

Non-stick properties are embedded into the coating itself. Great news for fans of the brass brush. You are free to scrub ObXidian to your heart's content. Cold pulls are also on the cards. These were two of the main focuses of customer feedback about Nozzle X, and we took this on board when creating ObXidian. Check out this guide for more info on our recommended cleaning techniques.
We also want to make it abundantly clear that not all DLC coatings are equal. We could have just used a standard ‘off-the-shelf' DLC coating. That's not how we do things at E3D though. Our Engineers have spent years researching and testing DLC coatings in search of the perfect composition for our users’ needs. E3DLC™ is the culmination of all that hard work.

Generic DLC coated V6 Nozzle

E3DLC™ coated V6 Nozzle
These two photos were taken at exactly the same stage of a test print. The same G-code and filament was used for both tests.
Wear Resistance
Strong wear resistance is essential when printing with abrasives, as fibre-filled filaments can ruin a Brass nozzle in hours. With a wear resistance that is orders of magnitude higher than any other E3D nozzle, ObXidian is really hard.
To achieve this uber-hardness, ObXidian relies on two things:
- First, a hardened steel insert. Retained in the copper body of an ObXidian nozzle, this alone offers great wear performance.
- Second, and the (literal) icing on the cake is E3DLC. It's certainly not just there for its non-stick performance. As we’ve already mentioned, DLC coatings are extremely hard.

The ObXidian Assembly. Prior to E3DLC™ coating

No Unicorns were harmed in the making of ObXidian!

Except for this one! This is the Revo 'ObxidiCorn' designed by Thorsten Hartmann
...what took you so long?
Here’s an extract from our recent ObXidian Update blog, if you’re interested in knowing more, it’s well worth a read. There are a lot of complex processes involved in making a product like ObXidian. If one process changes even subtly, work must be done to make sure all the others are still fine. Sprinkle in ludicrous lead times and you have a recipe for major delays. There have been countless occasions when we couldn’t get good parts or sometimes any parts at all.
...but why didn’t you just make Revo Nozzle X?
People will always want the latest technology. Rather than bring our older Nozzle X to the Revo line-up, we wanted to put our full focus into making ObXidian a reality and at the time, we had every reason to believe that V6 ObXidian would launch before the Revo ecosystem, with Revo ObXidian just after. If we’d have known it would take this long, we would have done things differently, but it’s easy to say that in hindsight!
Where did the name come from?
Planning a new product ecosystem back in 2020, we realised we needed new names to describe the many new variants in the pipeline. Obsidian, Sanjay informed us knowledgably, was highly sought after by early man, with many uses, including cutting, and the shaping and finishing of objects. Seems appropriate, right? During the development of our unique E3DLC coating, we discovered that the exact coating method that produced the properties we needed, also happened to bear a striking resemblace to rainbow & fire obsidian. It was meant to be. The final piece of the puzzle was the ‘X’, which pays homage to ObXidian’s predecessor, Nozzle X.
By the way, ObXidian can just be pronounced obsidian. No need to put emphasis on the X!

Fire Obsidian, a variety of iridecent obsidian. Image Source.

There are some visual similarities between Fire Obsidian and ObXidian Nozzles
We’ve got 0.25, 0.4, 0.6 and 0.8 mm Revo ObXidian™ Nozzles available to buy right now! Do you have V6 or Volcano nozzles? You can also upgrade to V6 ObXidian and Volcano ObXidian Nozzles.
You need to print faster? Check out our new Revo ObXidian™ High Flow Nozzles available in 0.4, 0.8, 1.0, 1.2 and 1.4 mm nozzle diameters.
Buying outside the UK? Avoid additional charges and lead times by ordering from your local E3D Reseller. Looking for more technical info? Documentation for ObXidian is available on the E3D Help Centre. If you have further questions, we’re available to chat on Discord or social media. Don’t forget to follow our blog for the latest E3D news and updates!
Frequently Asked Questions
If you've got questions about ObXidian, you should find the answer here!